The Benefits of Automotive Plastic Injection Molding for Metal Fabricators
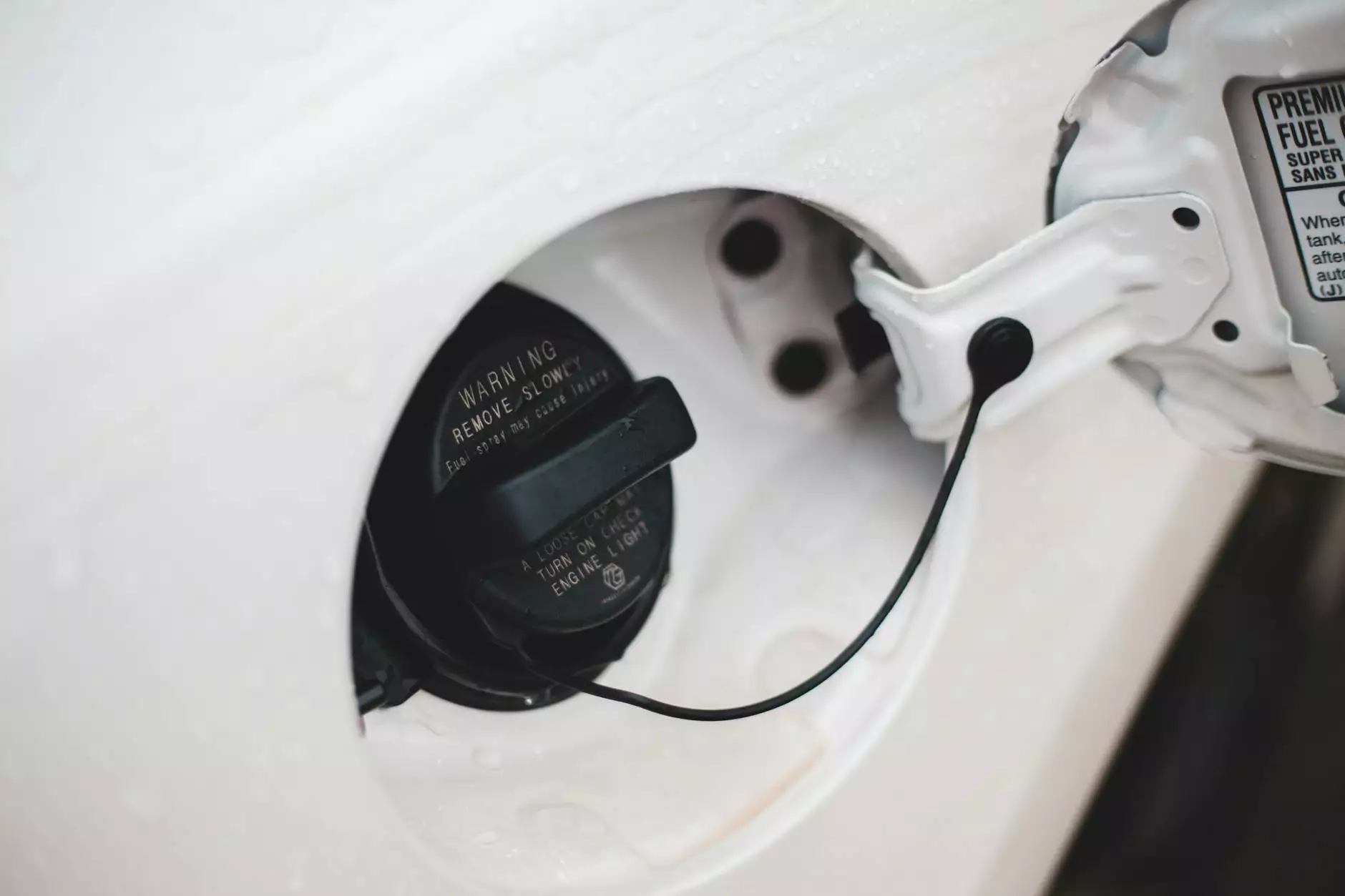
Introduction
In the world of metal fabrication, businesses are constantly seeking innovative solutions to meet the ever-changing demands of their customers. One such solution is the adoption of automotive plastic injection molding. This cutting-edge technology has gained significant popularity in recent years, and for good reason. Metal fabricators who embrace plastic injection molding can reap numerous benefits that enhance their productivity, efficiency, and overall success.
Understanding Automotive Plastic Injection Molding
Before diving into the advantages, let's briefly explore the concept of automotive plastic injection molding. This process entails injecting molten plastic into a custom-designed mold to manufacture high-quality plastic components used in automotive applications. It allows for precise and repeatable production, resulting in components that are durable and reliable.
Advantages of Automotive Plastic Injection Molding
1. Versatility
Automotive plastic injection molding offers exceptional versatility for metal fabricators. This technology allows for the production of complex shapes and intricate designs that would be otherwise difficult or impossible to achieve with traditional metal fabrication techniques. The ability to create lightweight, yet strong, plastic components opens up new possibilities for automakers, enabling them to enhance fuel efficiency and overall performance.
2. Cost-Effectiveness
In today's competitive business landscape, cost-effectiveness is crucial for any metal fabricator. Automotive plastic injection molding offers significant cost advantages compared to traditional metal fabrication methods. The process can be automated, minimizing labor costs and reducing the overall production time. Additionally, the scrap material generated during the production can be recycled, further reducing waste and expenses.
3. High Production Efficiency
Efficiency is paramount in the automotive industry, and automotive plastic injection molding delivers just that. The process allows for high-speed production of plastic components, meeting strict deadlines while maintaining superior quality. With quick cycle times and minimal setup requirements, metal fabricators can streamline their production processes, resulting in increased output and improved overall efficiency.
4. Enhanced Product Quality
Quality is a non-negotiable aspect for metal fabricators aiming to satisfy their automotive clients. Automotive plastic injection molding produces components with exceptional accuracy and consistency. The high-pressure injection ensures that each piece created adheres to the precise specifications outlined in the mold design. This technology offers tight tolerances, excellent surface finishes, and eliminates common issues associated with traditional metal fabrication, such as warping or deformities.
5. Design Flexibility
Automotive plastic injection molding grants metal fabricators unparalleled design flexibility. The ability to rapidly prototype and iterate designs allows for efficient product development and customization. Design enhancements can be easily implemented without costly tooling changes, enabling quicker response times to market demands and fluctuations. This flexibility is particularly valuable in the fast-paced automotive industry, where staying ahead of the competition is a constant challenge.
6. Improved Durability
When it comes to automotive applications, durability is a top priority. Automotive plastic injection molding offers exceptional durability, as it produces strong and impact-resistant plastic components. These components can withstand harsh environmental conditions, extreme temperatures, and the wear and tear associated with automotive use. The ability to incorporate reinforcement materials, such as fiber or additives, further enhances the durability and strength of the final product.
7. Reduced Weight
The automotive industry is continuously focused on reducing vehicle weight to enhance fuel efficiency and reduce emissions. With automotive plastic injection molding, metal fabricators can contribute to this weight reduction. Plastic components are typically much lighter than their metal counterparts, allowing automakers to achieve weight savings without compromising performance or safety. By incorporating lightweight plastic components into their designs, metal fabricators can help automakers meet their sustainability goals.
Conclusion
As metal fabricators strive to stay competitive in the automotive industry, embracing innovative technologies becomes essential. Automotive plastic injection molding provides a host of benefits that cannot be overlooked. Its versatility, cost-effectiveness, high production efficiency, and enhanced product quality make it a game-changer for metal fabricators looking to meet the evolving needs of their customers. With design flexibility, improved durability, and reduced weight, this technology empowers metal fabricators to deliver top-notch automotive components that drive success in a rapidly changing market.