Titanium Screws Manufacturers: Innovations and Quality in Fasteners
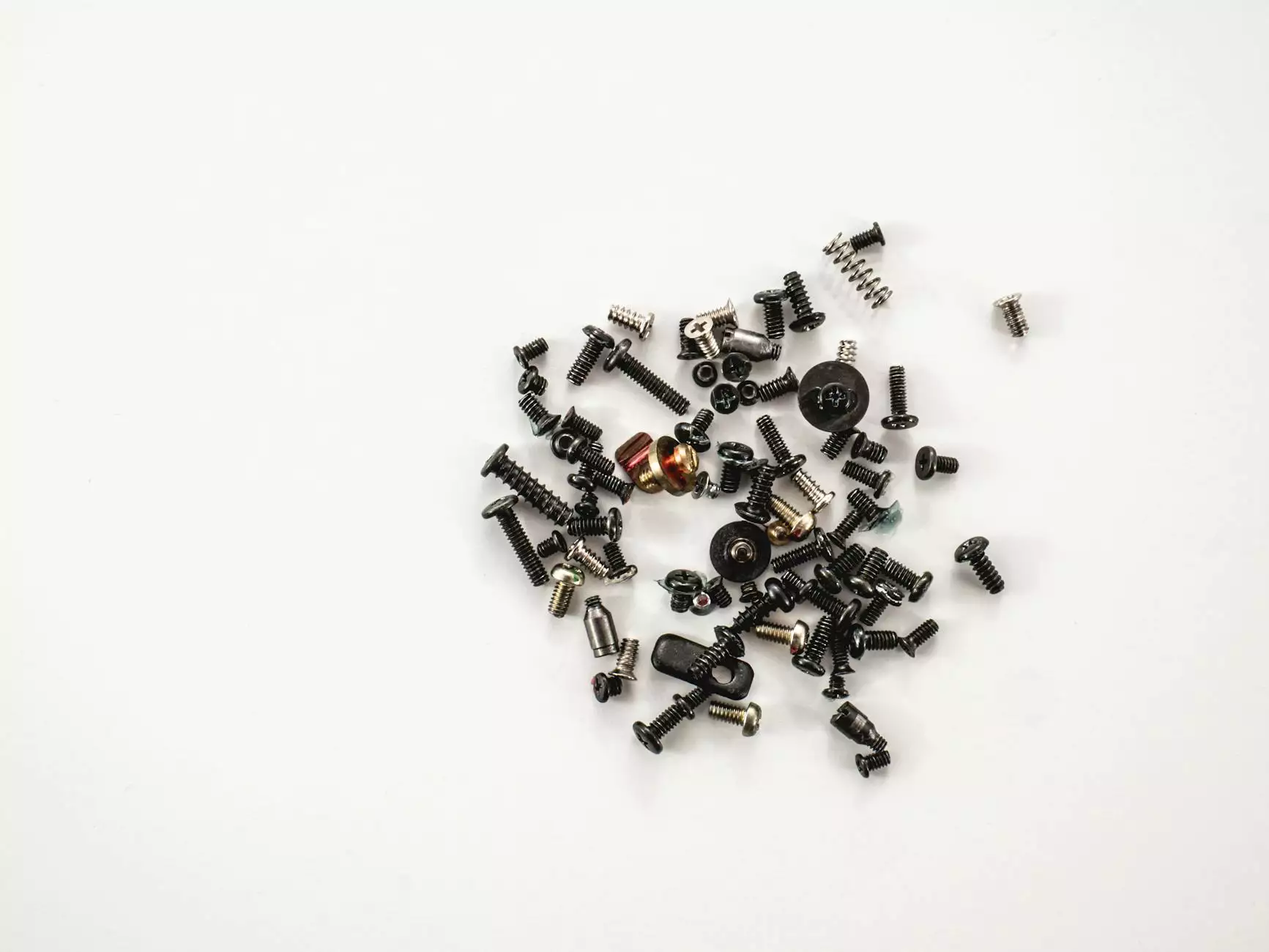
In today's competitive market, titanium screws manufacturers are at the forefront of producing superior fasteners that cater to a variety of industries. The unique properties of titanium, including its strength, lightweight nature, and corrosion resistance, make it an ideal material for fasteners used in sectors ranging from aerospace to medical devices. This article delves deep into the world of titanium screws, exploring the manufacturing processes, benefits, and the key players in the industry, especially focusing on the renowned titanium bolts as a leading titanium fasteners manufacturer.
Understanding Titanium Screws
Titanium screws are specialized fasteners made from titanium, an element known for its exceptional biocompatibility and mechanical properties. They are used widely in applications where performance and reliability are critical. Some of the significant characteristics of titanium screws include:
- High Strength-to-Weight Ratio: Titanium is incredibly strong for its weight, which makes it an unparalleled choice for heavy-duty applications.
- Corrosion Resistance: Titanium naturally forms a protective oxide layer, which safeguards it against corrosion from environmental factors.
- Biocompatibility: This property makes titanium ideal for surgical implants and medical devices, where body compatibility is crucial.
- Heat Resistance: Titanium can withstand elevated temperatures, making it suitable for high-temperature applications in aerospace and automotive industries.
The Manufacturing Process of Titanium Screws
Producing titanium screws involves several intricate steps that ensure quality and precision. Here’s an overview of the typical manufacturing process used by titanium screws manufacturers:
1. Material Selection
The first step involves selecting high-grade titanium material, often in the form of titanium alloys such as Ti-6Al-4V, which offers excellent mechanical properties.
2. Machining
Once the material is selected, the titanium is machined into the desired screw shapes. Advanced CNC (Computer Numerical Control) machining technologies are commonly used to achieve high precision in dimensions.
3. Surface Treatment
Many manufacturers employ surface treatments to enhance the durability of titanium screws. Processes include:
- Anodizing: This creates a thicker oxide layer on the surface, increasing corrosion resistance.
- Shot Peening: This technique improves fatigue strength by introducing compressive stresses on the surface.
4. Quality Control
Quality control is paramount in the manufacturing process of titanium screws. Manufacturers conduct rigorous testing, including:
- Tensile Testing: To determine the strength and ductility of the titanium material.
- Corrosion Testing: To ensure the screws can withstand harsh environments without degrading.
The Importance of Choosing the Right Manufacturer
Selecting a reliable manufacturer is vital for ensuring the quality of titanium screws. Here are some reasons why one should choose established titanium screws manufacturers like TitaniumBolts:
- Expertise and Experience: Established manufacturers have years of experience and expertise in producing high-quality titanium fasteners.
- Customization Options: They often offer customized solutions to meet specific project requirements.
- Certifications: Look for manufacturers with ISO certifications or other quality assurances that guarantee adherence to international standards.
Applications of Titanium Screws
Titanium screws are used in various applications, highlighting their versatility and reliability.
Aerospace Industry
The aerospace sector is a significant user of titanium fasteners due to their lightweight and strength properties, which contribute to fuel efficiency and performance. Components such as engine mounts, airframe attachments, and landing gear all utilize titanium screws.
Medical Devices
In the medical field, titanium screws are utilized in implants, dental products, and surgical instruments. Their biocompatibility ensures that they are safe for long-term use within the human body.
Automotive Engineering
High-performance vehicles often incorporate titanium screws in their construction to reduce weight while maintaining strength. This contributes to better speed and fuel efficiency in racing cars, sports vehicles, and luxury cars.
Benefits of Using Titanium Screws
The benefits of employing titanium screws over other types of materials, such as steel or aluminum, include:
- Reduced Weight: The lightweight nature of titanium can significantly lower the overall weight of products without sacrificing performance.
- Long Lifespan: Titanium’s resistance to wear and corrosion results in components that outlast those made from other materials.
- Reduced Maintenance Costs: Longer-lasting screws reduce the need for frequent replacements and repairs, thereby saving costs in the long run.
Future Trends in Titanium Fastener Manufacturing
As the demand for titanium fasteners grows across various sectors, manufacturers are innovating to improve efficiency and sustainability. Key trends in the industry include:
Use of 3D Printing
3D printing technology is revolutionizing the manufacturing process by allowing for rapid prototyping and customized designs. This technology can reduce waste and lower production costs.
Sustainability Initiatives
With an increasing focus on environmental impact, titanium screws manufacturers are adopting sustainable practices in their production processes, including recycling titanium scrap and reducing energy consumption.
Conclusion
In conclusion, titanium screws manufacturers play a crucial role in the production of high-quality fasteners that cater to diverse industries. With unique properties such as corrosion resistance, lightweight, and strength, titanium screws are indispensable in modern applications ranging from aerospace to medical devices. When choosing a manufacturer, consider factors like experience, quality assurance, and customization capabilities to ensure optimal results.
As the industry evolves, staying informed about advancements in manufacturing processes and material science is essential for businesses that rely on these critical components. Whether you seek specific applications for aerospace, medical, or automotive purposes, trusting reputable manufacturers like TitaniumBolts can make all the difference in achieving your project goals.