CNC Machining Parts: The Backbone of Modern Metal Fabrication
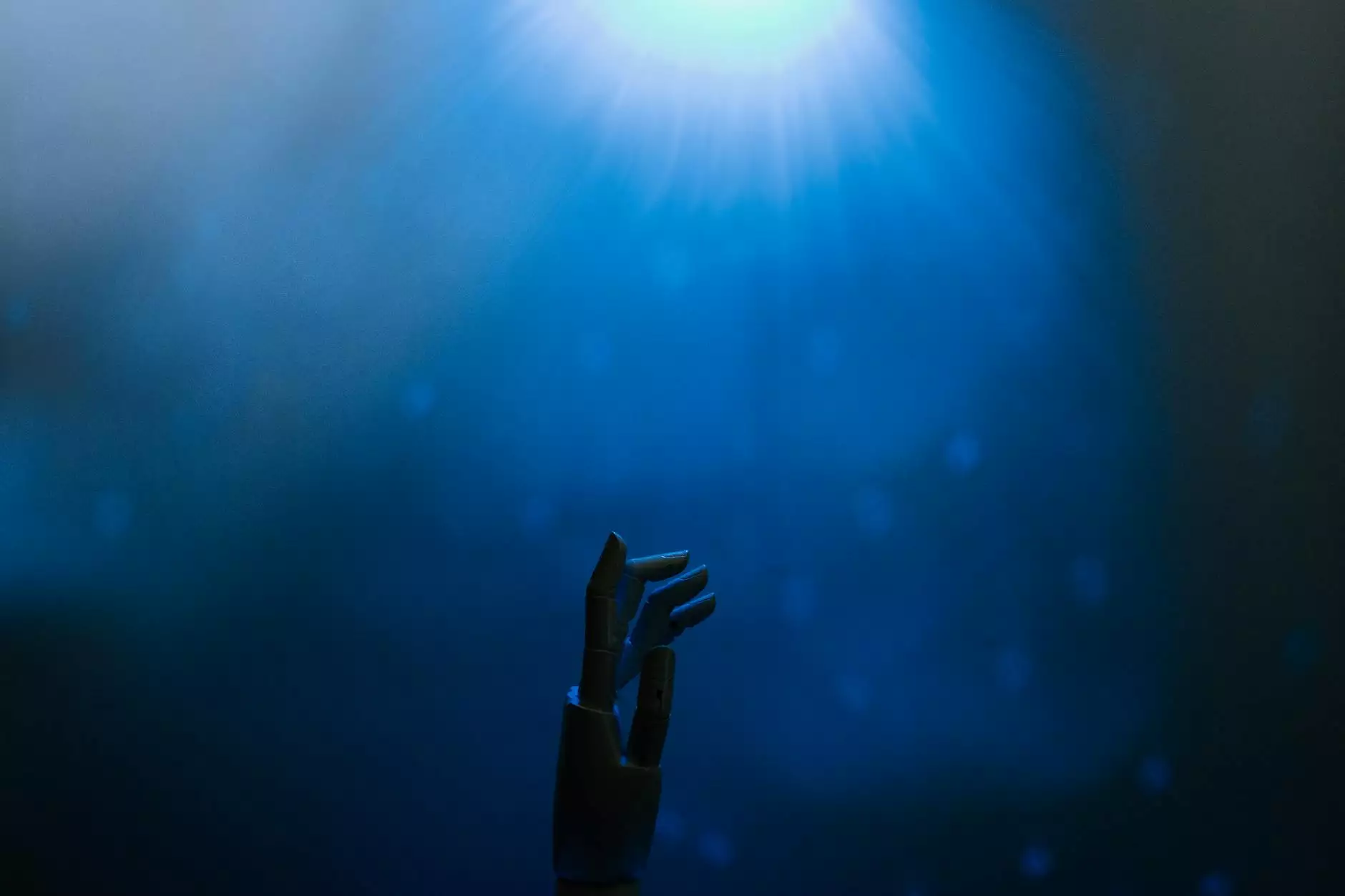
CNC machining parts are at the forefront of metal fabrication technology, offering precision, efficiency, and versatility. The CNC (Computer Numerical Control) process allows manufacturers to produce complex components with a high degree of accuracy. In this article, we will delve deep into the world of cnc machining parts, exploring their significance in various industries, the intricate manufacturing processes involved, and the transformative impact they have on the metal fabrication landscape.
Understanding CNC Machining
CNC machining is a manufacturing process whereby pre-programmed computer software directs the movement of production equipment. The process is employed to control a variety of complex machinery, including grinders, lathes, mills, and routers. This technology enables the creation of parts that are repeatable in quality and precision, making it the preferred choice for manufacturers across numerous sectors.
Key Components of CNC Machining
The efficacy of cnc machining parts is largely contingent on several key components:
- CNC Machines: These include CNC mills, lathes, and routers, all programmed to cut materials with exceptional precision.
- CAD Software: Computer-Aided Design (CAD) software is used to create 2D and 3D designs of parts before manufacturing.
- CAM Software: Computer-Aided Manufacturing (CAM) software translates CAD designs into machine instructions that the CNC machine can execute.
- Material Types: Various materials such as metals, plastics, and composites can be machined, each requiring specific techniques and tools.
The Manufacturing Process of CNC Machining Parts
The process of creating cnc machining parts can be broken down into several key stages:
1. Design Phase
The journey begins with the design phase, where engineers and designers create detailed models using CAD software. These models are essential for precise machining and ensure that all specifications are met.
2. Tool Path Creation
Once the design is finalized, CAM software is used to create detailed tool paths. This programming defines how the CNC machine will move to achieve the desired cuts and shapes, optimizing speed and accuracy while minimizing waste.
3. Material Selection
The choice of material is crucial as different metals and alloys possess varying properties. Common materials used in CNC machining include:
- Aluminum: Known for its light weight and resistance to corrosion.
- Steel: Offers strength and durability, making it suitable for heavy-duty applications.
- Brass: Highly machinable and often used for intricate parts that require high precision.
- Plastic: Used in cases where metal is unnecessary or where weight savings are critical.
4. Machining Process
During the machining process, CNC machines are programmed to execute the cutting, drilling, milling, or grinding based on the tool paths created earlier. Multiple tools may be used throughout this process to achieve different features, enhancing the overall versatility of the finished part.
5. Post-Processing
After the initial machining, parts may require additional post-processing to meet specific tolerances, including:
- Polishing: Used to improve surface finish.
- Coating: Provides enhanced durability and protection from corrosion.
- Assembly: Parts may be assembled into larger systems or components.
Benefits of CNC Machining Parts
The adoption of cnc machining parts in various industries has resulted in numerous advantages that contribute significantly to operational efficiency and product quality:
Precision and Accuracy
One of the primary benefits of CNC machining is its ability to produce parts with remarkable precision. This is crucial for applications in industries such as aerospace and automotive, where tolerances can be incredibly tight.
Scalability
CNC machining allows for rapid scaling of production quantities. Whether creating prototypes or large production runs, manufacturers can easily adjust processes to meet changing demands without compromising quality.
Reduced Labor Costs
Automation in CNC machining reduces the need for manual labor, thereby decreasing overhead costs. Operators can oversee multiple machines simultaneously, enhancing productivity.
Flexibility
CNC machines can be programmed to create a wide variety of parts, making them highly versatile. This flexibility allows manufacturers to diversify their offerings and adapt to changing market needs.
Applications of CNC Machining Parts
The versatility of CNC machining has led to its widespread use across various industries. Some notable applications include:
Aerospace Industry
The aerospace sector relies heavily on CNC machining due to the stringent safety and performance standards required. Components for aircraft engines, fuselage parts, and landing gear are often produced via CNC machining for their superior strength-to-weight ratios.
Automotive Industry
In the automotive industry, cnc machining parts are used for both prototypes and end-use parts. Applications range from engine components and transmission systems to gear shafts and brackets.
Medical Devices
The medical industry benefits from CNC machining's ability to create highly complex components in materials that must meet specific biocompatibility standards. Surgical instruments, orthopedic implants, and dental devices are commonly produced using CNC technology.
Consumer Electronics
In the consumer electronics sector, manufacturers use CNC machining to produce casings, brackets, and internal structural components, ensuring quality and performance in packed devices.
Choosing the Right CNC Machining Parts Supplier
When seeking a supplier for cnc machining parts, it is essential to consider several key factors to ensure quality and reliability:
Quality Assurance
A reputable supplier will have quality management systems in place, such as ISO certification, which ensures that every product meets or exceeds industry standards
Experience and Expertise
Look for suppliers with a proven track record in CNC machining. Experienced manufacturers are more likely to understand complex requirements and meet specific industry standards.
Technology and Equipment
Modern CNC machines and equipment lead to better precision and capabilities. A supplier with the latest technology can offer better results in terms of quality and efficiency.
Customer Service
Effective communication and support are crucial throughout the production process. Choose a supplier that prioritizes customer satisfaction and provides consistent and clear communication.
Conclusion
CNC machining parts represent a cornerstone of contemporary metal fabrication. Their remarkable benefits, from precision and flexibility to scalability and cost-effectiveness, are pivotal in driving advancements across various industries. By understanding the intricacies of CNC machining, manufacturers can make informed decisions that enhance their production capabilities and ensure the delivery of high-quality products. As CNC technology continues to evolve, so too will the possibilities for innovation in metal fabrication, making it an exciting time to explore the world of cnc machining parts.
For businesses looking to enhance their production capabilities and ensure quality in their manufacturing processes, DeepMould.net stands as a leader in the metal fabrication industry. Our commitment to excellence and innovation in crafting high-quality CNC machining parts ensures that your projects are completed with the utmost precision and care.